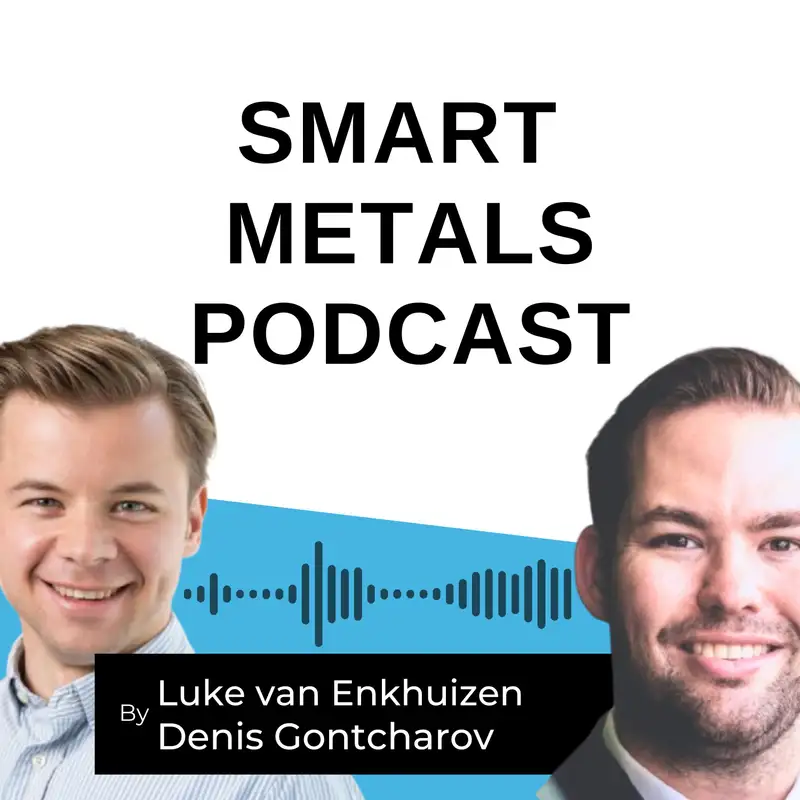
Unifying Manufacturing with Unified Namespace: A Conversation with Brian Pribe
Denis: Welcome to a new episode
of the smart metals podcast.
I'm your co host Dennis,
and I'm here with,
Luke: Luke van Enkhuizen.
Denis: and today we have a very
special new guest on our episodes.
Brian Pribe, welcome to the episode.
Brian: Hi, how are you?
Denis: good.
you here.
Brian: Good.
Denis: So Brian, I was thinking the best
way to kick off this episode is to first
give a good introduction about yourself.
Focusing on your background and your
personal journey in manufacturing.
Brian: Yeah.
So I'm Brian Pryby.
I'm the founder and president of Mock
Controls, and we're based out of Toledo,
Ohio, and pretty much I've started
out in this industry back in 2018.
Working for a systems integrator,
mostly started off doing, system
designs or more mechanical designs.
Then we eventually, worked into doing a
lot of the wiring of the panels and then
the actual engineering of all the control
systems to doing the programming, doing
the fabrication, the installation, the
final sign off the projects and stuff.
Works for some other integrators.
And then eventually wanted to start my
own then, eventually started getting
into this unified namespace topic.
And ever since been working towards that.
Denis: Interesting.
So is it fair to say you come
more from the hardware side?
Brian: Yeah, definitely.
On the hardware and machine building side.
Absolutely.
Um,
Luke: Interesting.
Well, actually I come from the workflow
field, from the shop floor itself.
That's why I started and then I
became an engineer actually designing.
Parts for customers.
So I really come from the
fabricator side of things.
The machine building is
really my interest though.
Denis: So Brian, you mentioned that
you discovered a unified namespace.
How did that happen?
Were you looking for a
solution to a problem you had?
Or was it more of an accident?
Brian: I was mostly just trying to stay
on top of the industry and really tried
to improve my skills with everything.
And on YouTube, like as everybody
else does, they're trying to
look for new things to look for.
one of them was a video
from Walker Reynolds.
And I think it was about, IOT in general.
And since then, I've just been
consuming all of their podcasts, all the
videos that they had out at the time.
And then I joined of the workshops
starting out with, and since then I've
just been involved with their mastermind
program and from them, applying it and
then changing kind of my business model
towards more, towards this new approach on
how to actually get information from, the
plant floor and use it in a better way.;
Denis: And I guess you mentioned
that you worked a bit on a project,
either for a client or for yourself.
Can you talk a bit more about that?
Brian: Yeah.
So some of the things that we've
been working towards with the unified
namespace, a lot of it is, as you guys
know, as you guys are also in the, a
lot of the, different communities with
it, it's a very difficult architecture
to kind of start up and to actually
start kind of understanding with it.
So the base premise with it is
using an MQTT broker as your current
state for the business and all the
events that happen that business
go in there in a structured manner.
So everything is now available, but part
of the problem is that you got to take
all the history of all those events.
You got to save all so
that you have them all.
You can do more analytics with it too,
but it's not a very easy approach.
And when we're trying to apply this for
a lot of manufacturers, a lot of them
aren't going to have the skill sets.
to get one of these
instances set up for it.
I mean, we're dealing with kubernetes,
we're dealing with Helm charts,
we're dealing with multiple,
different applications stacked
and integrated with each other.
It's going to be very difficult for
even a small team to be able to handle.
So when we were looking around
in the market and seeing what's
available, united manufacturing
cope was kind of one of the few.
That kind of understood what
the problem was with the unified
namespace and the architecture.
And I believe that they came with the
right approach on how to solve it.
And then at the end of the
day, they turned around and
made it into a FOSS solution.
So now everybody is allowed to use it.
And that's where we're now coming in
on wanting to take up on the work that
they've done and start applying it
to as many manufacturers as possible.
So what I think, UMH gets right
a lot about it is the combination
with MQTT and with Kafka.
So one of the problems with
manufacturing is you need to be
able to connect all your devices.
There can be thousands of different
machines say like a large manufacturer
or medium sized manufacturer.
And the majority of those
machines are not connected.
Into the plant, network.
when we're looking at this problem
and trying to understand, okay, what
are the benefits of this application?
What are the benefits of that app?
Kafka falls, short on device connectivity.
It doesn't MQTT does that really well, but
it doesn't have very much else to it other
than it just being a broker for devices.
So combining both the technologies of
and QTT, you get that device connectivity
and the history of all the events
that have happened for it as well.
So I think just that approach already
that handles the majority of the
problems with the unified namespace.
No really need for connecting to
a historian with it and trying
to get all the benefits that
Kafka already does give you.;
Denis: Yeah, I agree.
That was also one of the
observations I had about the clever
combination of Kafka and MQTT.
Can you just comment to, highlight the
problem about what type of clients are
you talking about, the talents of devices?
Are they more, job shops?
Are they more discrete manufacturers,
continuous manufacturers in English?;
Hmm.
Well, I mean, it very much
so like very broad scope with
a majority of manufacturers.
So this can apply with discreet.
With a continuous, or batch
type, manufacturing processes.
So if we're talking about
discrete, there's plenty of work
cells that manufacturers have
for assembling all the different.
Pieces and parts of
their product and stuff.
And the majority of those machines
still aren't connected as well.
And then when it comes to
say like a continuous batch,
there's some very expensive
machines, say like some furnaces.
where it's a continuous cycle of parts
coming in, parts coming out, and they
have some very complex furnace controls
on monitoring the temperature, monitoring
the humidity and everything about it
and the time that the parts are in it.
;
But none of that information
goes outside of it.
I even had this conversation this week
with, a machine builder for furnaces.
;
And this was one of the critiques
on it is that they deliver
this million dollar machine.
It does a lot of great
things for the manufacturer.
However, the manufacturer
doesn't do anything with the
information inside of it.
So they don't take any of the
history about any of the process
values that are being generated.
They don't try to relate it with any of
the batches, say like, with production
orders, nothing about the machine
gets out of its own domain....;..
And so, and why is that?T?
Brian: Oh, It's hard.
Well, it's not just hard to connect.
I mean, in the U.
S.
We have a little bit of a
problem with like Allen Bradley.
It's a very good protocol.
It's very lightweight protocol, but
to be able to connect to it you kind
of need some very expensive drivers.
it's not very open at all.
And that's just one app, one side of it.
So the licensing costs for it.
And then the other side to it is that,
manufacturers really don't have a
very good way of saving this sort of
stuff aside from just creating another
database that ends up being a data silo.
So it's, you just end up with
so many of these disparate data
sources that none of them get
linked into each other and nothing.
It is trying to talk with one another.
And that's always sent teams to be the
problem with a lot of manufacturing.
Denis: Would you say the
same is true for Europe?
Luke, it sounds familiar.
Doesn't it?
Luke: It's similar in a way that
it rhymes of course, but it's
different in a way in the details.
But yes, I think the biggest challenge
is not per se that the machines
don't have the connectivities.
It's the fact that most.
Users of the machines, the
manufacturers themselves that use
that equipment, not even remotely
aware how many, sensors and, computer
systems are actually in their plant.
They have no idea of what's even
going on inside of the equipment
they use on a daily basis.
So I think it even starts there.
It's a step before that, example in
CNC world, you have CNC machines.
These machines have way
more than an on off, right?
They a vast amount of data and, being
aware what's in it in the first place.
I think it's already the first step.
Denis: So let's cover focus a bit
more on the unified namespace.
I tend to agree that it solves the
problem of keeping data in one place,
but at a discussion with Luke today,
a bit earlier about that it's still
very difficult to connect different
machines to the unified namespace.
There's just so many different machines.
Is there a way to perhaps systematize
this somehow, or will this
always be a big integration work?
What do you think?
Brian: So , I think that there's been
a lot of newer solutions coming out.
There's been a lot of better means of
applying softwares as well on the edge.
So either using Docker containers
to deploy on edge devices.
To connect to the machines and be
able to get the information out,
because a lot of machines nowadays,
they don't really have MQTT built in.
They rarely can have
A-A-O-P-C ua server to it.
And if it is, the configuration
for that is interesting.
The means of which to connect a lot of
the machines still requires another,
gateway, to get into a unified namespace.
But the benefit MQTT is that
eventually it can really connect
to any type of small device.
So we're talking things as small
as a light bulb being integrated
with the entire business.
So with that type of capability and
ability, we really want to utilize that
and have that be the minimum technical
requirement for any sort of device.
Or machine to connect to it.
Denis: I think you have an
interesting law coming up, right?
In Europe Luke, I think it's
called the European data act.
Luke: Yes, we were
talking about this today.
So in Europe, you think differently
than the rest of the world.
I always say like in Europe, we like
to, you know, make a system with a
law and then push it down on all the
member countries in a way that we have
a certain guideline as a certain law,
but Nobody really understands what
it really means, but it sounds good.
And then we kind of try to
make something out of it.
And one of these things that we are now
trying to wrap our heads around, Dennis
and I, is that there's this thing called
the European Data Act, which states
that it should be easier for those
that have a device to access this data.
And if you buy a machine, a piece
of equipment or anything that if
that generates data, you should be
able to access it and make it yours.
Kind of, that's the very
simplified explanation of it.
And so we are, we're working on this and
it seems that this is actually starting
to gain some ground that we are saying,
okay, it seems to be kind of obligatory
for manufacturers to then open up their
devices, or at least be very transparent
about what they do with it or not, and
what it costs for you to access it.
So, yeah, some positive developments
going on here, I think, but still, I
think the challenge will be the actual
definition of a piece of equipment of
what kind of signals and what kind of
events it generates, and how do you
capture those in a standardized manner
so we don't have to reinvent the wheel
for each individual piece of equipment.
Right.
so that's the kind of, I
think it's still a big puzzle.
Brian: Are there any application
examples of that being used
right now that you know of?
Luke: Application examples in which way?
Brian: Yeah.
So like you're seeing like people starting
to take up a lot more with this law,
have you seen it like come into fruition
in some or like, are there any examples
of any manufacturers trying to do that?
Or what are the conversations
that seem to be going on about it?
U S we don't really, we don't
have this type of approach.
Usually it becomes a customer has
some sort of mandate about what they
want and you just need to give it to
them at the end of the day, either
that, or you don't get the business,
Luke: Yeah, it's very similar, I think,
in a lot of respects to what we did
with GDPR, with the data protection
laws against like customer data,
was a major development especially
in the consumer space, right?
So cookie banners, as you might know, in
Europe, whenever we visit website, we see
a cookie banner, and it's very annoying.
We have to put a lot of, check boxes
and all kinds of places to confirm that
we actually want to share our data.
I think that we see a similar movement
in the manufacturing space now where we
will first have a lot of bureaucratic
procedures and eventually it will lead
to better practices when it comes to.
OT data to acquire
so examples of that, you can see
the shift already that indeed, when
you go to conferences, you see that
manufacturers, so not per se the end
users, but the machine builders, the
equipment, builders, those are now
advertising with their connectivity.
Actually selling the same machine with a
new connectivity layer as a new products.
It's not the best, but
Brian: but it's an approach
in the right direction.
Luke: Yeah.
That's what I see at least.
What are you about to do Dennis?
Denis: I think it's
still too early, right?
The law only goes into effect
at the end of this year or
25 Year.
I also noticed that, for example, I had
a discussion with a potential client
in Germany who was trying to extract
data from about 30 big machines.
And the only way to do it was through
OPC UA, for which they had to purchase
an additional add on license per machine,
costing about 4, 500 US dollars per year.
So that's more than 100k dollars
spent every year just to get data.
But the customers seem to be okay with it.
They're more like, well, it is what it is,
as perhaps an American would say, there's
no way we're going to buy that machine.
In Europe, they seem to be more
at the mercy of the vendors.
Brian: I mean, typically if it's at
the very beginning of the engineering,
manufacturers do want to exactly what
they want, but towards the end of it,
when you're dealing with like a bit of a
brownfield, example, manufacturers tend to
just have to deal with whatever they have.
And then the offers kind of brought
forth for them was like, Hey, we can
connect this machine to an OPC server.
It's just going to cost a Kepler license.
And at that point, it's like, Hey, it's
either that, or you're kind of out in
the wind, trying to pick whatever else
other solution may be out there for you.
Denis: Yeah.
Brian: So it's either you go with
an industrial grade one, or you go
with an open source one, but for a
lot of manufacturers, Especially for
the medium to a large size, we're
dealing with ones that have already
three shifts working and they really
need a solution that doesn't break
above, I think, 10, 000
tags or something like that.
Denis: So let's focus a
bit more on your project.
If you're allowed to talk about it, you
mentioned that it runs on a Raspberry Pi.
Brian: So we've been talking to this whole
time about trying to get manufacturers
to adopt this new technology.
But we mostly have been talking about
examples with larger manufacturers,
but with smaller manufacturers, we're
talking about companies that produce
between 1 to 5 million in revenue, they
have between 5 to 20 employees, and
they have between 5 and 20 machines.
So most of those machines, they're like,
you know, CNCs, they're probably breaks.
They're just like two, like you're
going to have like two expensive,
one to two expensive ass machines.
And then everything else
is more rudimentary.
So like drill presses
sawmills and stuff like that.
So when we're talking about
the majority of manufacturers,
that's what they look like.
That's what the makeup
of that manufacturer is.
So when we're talking about what
are their needs, what do they
need to connect to their machine?
What does the price cap for them look
like on being able to adopt this?
We started to realize that the cost
of the hardware and the cost of the
software just to get them through
the front door is already very steep.
So, we want to be able to
bring this to everybody.
So we need to look for hardware
that is at that price point for
everybody to be able to afford.
So, we've been looking at Raspberry Pi
for those edge devices for that compute.
And we want that so that we can lower
that price down to a level that everybody
can be able to afford for their machine,
because nobody's going to be able to
look at a drill press and try to justify
a 2, 000 edge device for a drill press.
That only costs like 200 bucks, you know?
....
so it's kind of one of those
conversations of like, we really
do want to improve the process.
We want to get.
Every aspect of the manufacturing
process involved or connected, but
like, we're looking at, tools being
used and machines that really are
either very old, very brownfield.
Or they just don't justify much of the
cost to try to put the money towards
it, you know, at least when we're
looking at current solutions right
now, so if you're trying to put like an
HMI right next to a drill press using
current, offerings from the big vendors.
You're looking at spending, I
mean, north of 5, 000 for just
the licensing, let alone the
engineering that comes with it too.
And then we got to talk about
the management of these services
and these systems and stuff.
Who's going to be doing that.
And most of the time, these businesses
have between like one or two it
guys, and then maybe two to four
engineer types and everybody else.
Is more or less an
operator type of person.
And there's nothing wrong with
that for the manufacturer.
Everybody has a job type
for that specific reason.
But when we're talking about the
requirements of these types of systems,
you need a lot of it type people, involved
to maintain it and to keep it operational.
So that, you're able to extract the value
that this technology is able to bring you.
so what we're trying to do
is really lower that bar.
For manufacturers to be able to
have this, type of infrastructure
and lower the cost of the hardware
to make it accessible for them too.
Denis: Mm hmm.
Brian: So that's more or less the main
goal and why we've been trying to drive
in one of the projects that we've been
working on is with a edge raspberry
pi device that's been industrialized.
So we're really trying to look for
solutions for all the small manufacturers
to be able to get involved with it.
And that's why we've also picked
a united manufacturing hub.
Not only did they get it right, But
they also went the other direction,
and they open sourced it and made it
available for everybody to have it.
And that in and of itself, that's
already going to revolutionize the
industrial space, just with that alone!
Denis: Interesting.
Didn't you receive some pushback
from the manufacturer based
on some fear against FOSS?
Brian: So I think that it, as long as
it doesn't become a critical application
where their manufacturing relies on it.
So if it is something like in the
medical space with the batch recording
for a certain machine, they really
want that to be very up to snuff and
it makes sense because there's a lot
of legal liabilities involved with it.
But when we're talking about things
about, "Hey, we just want to know how
many parts were produced on this machine
and the machine has no connectivity.
"
People don't care about it.
People don't care whether
it's open source or not.
They just want that problem solved.
you know, for non critical
applications, open source all the way.
Start it, hell, even with
your proof of concepts.
Start with FOSS solutions.
It's not going to cost you anything.
It's going to at least push you into
that direction for the customer.
If it works, even better, it's free.
And then you can even contribute
to making that source better.
Your participation with using that open
source technology makes it better anyways.
So, we want to push manufacturers
in that general direction, anywho.
And starting off with a proof
of concept with FOSS solutions
already makes a lot of sense.
I would say it's just as long as
it's, once you start getting towards
more critical type of applications.
Then you start, then you really
need to look at the details and
see whether that solution is able
to provide that for you or not.
Denis: Yeah, that makes sense.
Let's do a bit more on the whole
approach that you're taking.
You mentioned obviously open source
and also an iterative small POC
concept, because I guess this whole
data story is still too new to
be completely understood from the
beginning to end, unlike automation.
So would you subscribe to
the approach where you always
start with a small use case?
You eventually scale up to the
whole factory, or would you say
that you need to have a UNS with
everything in it from the beginning?
Brian: If you really
want to get up to speed.
Yeah, sure.
You could take that approach of just
going up UNS all the way directly with it.
But I think with a lot of
manufacturers, they're still
trying to test the waters on it.
And the thing is with
implementing a unified namespace.
It tends to happen where you need to
change your business strategy with
it too, because what it unleashes
for you is the ability to have all
the information and all the events
that happen within your business.
Now that it's contextualized
and normalized, you can now do
analytics with it, and you can
Use all of that information, that
contextualized good information.
You can really dig very deep
into, the data and try to get
sort of analytical insights on it.
With precisions that other
systems aren't able to do.
So we're talking about giving you data
from everything that happened from the
very beginning of when you installed it to
the current state right now in real time.
many systems have not had anything
close to that ability the approach with
unified namespace is that you want to
normalize and contextualize everything.
Before it goes into the namespace.
So already that ETL process that a lot of
people have to do in data science before
they can get to any sort of good insight.
90 percent of that workload
already gets done before it
gets into the unified namespace.
So even at the real time state, it
gets done before the current state.
So it's already very
powerful in that aspect.
Now you get real time.
history and you can plug it into
various other systems as well.
Luke: Yeah.
Lots to uncover here.
Thank you so much, Brian.
this is very interesting.
So , we talk a lot about.
the differences between the approaches.
And I think that is very important to
make a significant shift in how you
try to solve your business challenges.
So for people that are interested in
making their first steps, so let's
say you are a manufacturer of midsize
and you hear all this and you're
saying, okay, this sounds great.
So there is a lot of movement
going in there, there's new
things possible for my company.
But where do I start?
what would be in your experience, the
best way to approach such a project?
what would be the first questions
to ask and the first conversation
to have in your experience?
Brian: With a lot of manufacturers, I
would say you got to start at kind of
like the very base of the business itself.
What is their strategy with using data?
Are they, do they have any
sort of strategy with it?
What's their plan with it?
If there isn't any at all.
You you're going to be starting off
very slow for the most part, because
we're talking about, different levels of
digital maturity within a manufacturer.
So a lot of people are, or a lot of
manufacturers aren't very mature when
it comes to the utilization of data
and the utilization of digital systems.
And we know that because, like,
majority manufacturers are
ran off of Excel spreadsheets.
majority of the time.
So if you're a manufacturer and everything
is ran off of excel spreadsheets and
you're not using any sort of databases
for taking in any of the events that
happened on the plane floor or you're not
trying to normalize basic transactions
between systems and stuff like that.
And everything is very human based.
It's going to be a very
big uphill battle for you.
And reason being is that you
have to change the way that that
business is operating today.
So instead of using Excel, instead
of printing out work orders for the
operators to, to utilize and stuff, you're
going to transition that all the way
towards using a digital infrastructure
that does all of that work for you.
That's going to be a massive step.
So what I would say for the companies
that are going to have a hard time
with this transition, you're going to
have to start with one machine, one
proof of concept and one strategy on
how to apply this for the business.
And, really start to understand
why this technology is important,
why you really need to have it.
And try to apply it at
least to one machine.
If you can get the value out of
that system off of just one machine.
And we've been able to see this
where we can get outputs the first
sealed pass output of the machine to
double because a lot of manufacturers
say like an example of the KPI OEE.
Majority of them don't track it when you
start tracking it, you realize that the
metrics on it is extremely low for you.
So just being able to show that
sort of information just available
for you is already the first step
towards it for a lot of manufacturers.
And I think that tends to be the
first step I would recommend because
majority manufacturers are nowhere
near ready for taking in this whole
new architecture and applying it to
every aspect of their business and
expecting their employees to know how
to use it and operate with it as well.
So there's a very big divide between the
manufacturers that get in the main fact in
the majority of manufacturers that don't
get it So that's why I think that majority
of them really ought to start with just
a proof of concept, one machine, start
off, get it right, see the value with it.
Then justify the next step.
Luke: Yeah, this is great.
Thank you so much.
one question on this topic.
We talk a lot about machines here, right?
The actual physical objects
that we are working with the O.
T.
Space.
So your experience in which ways
is also applicable to the I.
T.
Space to E.
R.
P.
Layers to business information, such
as orders and sales and maybe quoting
and contracts and stuff like this.
Have you seen any examples of that?
Being done effectively, how
these roles are being merged?
Brian: So we're talking
about integrating the ERP.
So the sales orders to transfer
over into work order, and then
for the warehouse management
system to be, integrated with it.
It tends to be a use case problem where
we start off on the plant floor, maybe
with one machine that they want to
connect And then It starts to go very
different based off the manufacturer on
what use case they want to approach first.
So most of the time it tends to be
ERP with getting sales order to work
orders but we've seen some that are
just a warehouse management systems.
So that tends to be like, you know,
it starts on the plant floor and
then it goes on to the next business
application with integrated on that.
Luke: All right.
I think it's very important to
acknowledge that the use case
varies per industry as well.
And I think per kind of business model.
So I always see it like you need
this in process manufacturing
as the board already suggests.
It's a process that has
to continuously run.
Right.
Brian: yeah,
Luke: That's the keep up me up.
And when it comes to your job
shop, you really are more into
mixing different types of orders
from different types of customers.
Brian: you're starting one project
and you're working and starting
on to the other one intervalling
Luke: yeah,
Brian: the two.
Luke: exactly.
And I think the machine uptime is not
as important as it is for a process
manufacturer, because in a job shop, the
value is mostly created on the flexibility
you can actually deliver to your customer.
if you want to be flexible, then
the same rules, I think apply.
It just becomes a lot harder to
then say, okay, I want to increase
my machine uptime because it
doesn't guarantee any more profits
Brian: Yeah.
it.
becomes less planning and more just
executing on it and being able to
manage that execution and then taking
those events and consuming them
so they're more consumption events
rather than trying to plan it all out.
Luke: Yeah, well said.
It's to say the difference
between push and pull, right?
Like
the, in the job shop environment
in extreme form, you are basically
only pulling like the machine
becomes free next order, please.
And then you really are trying to get
that thing in from the floor to see
what's the current status, if there was
any capacity at any machine right now.
And then you.
Put the work order in that machine that
has capacity right now and not tomorrow.
Right.
So that's a big difference.
But I see what you say there
and it's the same idea.
You can still do a very small proof of
concept for just a specific question.
for example, a planning board,
make your planning board digital.
That's already a great one.
I think
Brian: Yeah.
Luke: Yeah, so this is super interesting.
Just a little bit about yourself,
Brian, you mentioned your background,
what is your vision for the future?
Like, where do you think this
will move towards to, maybe
your business as part of that?
Brian: So we're looking on providing
more digital services for manufacturers.
We're looking to try to get this
type of technology in the hands of
as many manufacturers as possible.
And trying to work on as
many of them as we can.
Because; we see the potential of this
and we see what it can bring for a
lot of manufacturers and what it could
bring for the industry as a whole.
So like a lot of the problems with say
the generational gaps between like the
Gen Z years or the millennials, and
then you have your, the boomers and
the Gen Xs over off to the other side.
where the factory tends to be very
divided on the two where on the older
generations and we have a really hard time
trying to get the newer generations like
millennials and gen z into manufacturing
one of the massive aspects on it is
that it's very ancient going into
some of these manufacturing plants.
You look like, it looks like you jump
back into 1920s into some of these places.
And some of the buildings
are really that old.
And like the walls really have not
changed all that much from 1920.
But it's being used to
manufacturer's products today.
And so what we're looking at, like
the generation's got coming in, we
grew up off the internet and with
all these various digital skills
of plugging things in and like our
education being like digitally driven.
And then we come into a manufacturing
place and it's like, here's a paper,
you got to fill out this paper to hand
out to joe so that he knows what to
produce or what the dimensions are.
It's like, why are we doing it this way?
do we have to go back to?
the good old days of sticks and
stones to get all this information.
And that's one of the massive
problems with manufacturers
is that this is, everywhere.
This is on just about every
manufacturer and more specifically
for majority of small manufacturers.
So when we're talking about like the
problem going forward and what we
see in the future we see a lot of
manufacturers are going to struggle
a lot with, these businesses getting
older, the owners getting older and
trying to transition their business
and either selling it or handing it
off closing doors or getting acquired.
we're seeing a lot of them really
rough transitions because a
lot of them didn't plan it out.
You need to have multiple years
of experience in that industry
to know how to solve a lot of the
problems that kind of come up.
So say an example for systems integration.
We build a lot of control panels and
stuff like that, but it's almost a
bit of an art on how to wire a panel
and how to install all the wiring and
cabling that goes out to a machine.
Obviously to go with code, but to do it
in a way that makes it easy to maintain.
Once it's out there on
the plant floor and stuff.
So a lot of that type of
artwork as well is being left
off with the older generations.
And a lot of that information
isn't being transferred over
to the younger generations.
So we're looking at these 2 areas on,
like, not only is the current systems
that these old manufacturers are using.
It does not translate well to the
newer generations or the newer
ways of approaching business but
also the art that has been crude
over the years is now being lost.
And only sticking with
the older generation.
So we're losing that knowledge as well.
So we're going to see a big impact
for the small manufacturers and we're
looking to try to help them in that
transition and getting them up to
speed with the current trends of today.
Yeah,
Luke: I totally resonate to that.
You really made me chuckle when you talked
about the factory floor from the 1920s,
because it's exactly where I also started.
Actually started in metal company actually
sitting down and somebody gave me a piece
of paper and said, go make this part.
And then I was like, where?
Yeah, with that machine.
And if you don't know how to do it,
go ask the guy, he will tell you.
And I'm like, but, but I, funny
enough, I came actually also from
a background where I already made
websites since I was like 10.
For my family and my uncles and my
uncle had a car garage and I did
everything for him from the ERP
software and to all this stuff.
So I came there with this
piece of paper, man.
And I was like, and now,
yeah, go ask the guy.
And it was like, that's
not going to happen.
So, and then the first things I did
myself was to make my own like little
schedule, actually first Excel.
And then I built it into a
basic ERP from that frustration.
If you look closely at every factory,
you will see, indeed, they still have
the same layout and arrangement and
organization as they had in the 1920s.
The only thing that's changed right now
is the products and the frequency of
how fast things change, but in essence,
they have still a lot of similarities.
Only that if you can change
that, it's already so massive.
.
Brian: Yeah,
And then that first aspect is really
getting that machine connected.
So, I mean, a lot of the old
machines are still very good.
They do a fantastic job.
There's a reason why they've
been utilized for over 100 years.
They're still good machines.
It's just we have a problem on
not being able to connect with
it, and not be able to have it be
integrated with everything else.
That's really more or
less the problem with it.
Denis: Do you ever feel there's like
a skepticism maybe from the older
generation against the new stuff?
Like do you hear sometimes that, you
know, all this data, why do we need it?
You're just looking, it's
all smoke and mirrors.
There's nothing there.
Brian: I think with a lot of the new
machines have a ton of bells and whistles
and with it has its own complexity.
And that gives its own critique with it.
But when it comes to the data aspect,
you can only improve what you measure.
And if you're not measuring anything,
you're not going to improve at all.
So what we're trying to bring with
this approach and data is really
being able to measure every aspect
that we can, because the business
is really just a numbers game.
Business is all it is, is
just a bunch of numbers.
If you want a good business, you
need better numbers that have a
better profitability percentage.
That's really all that it's about.
And if you want to improve your
business, you need to, take in
the data on everything that's
happening within your business and
see what you can improve with it.
Cause if you don't, well,
you're not going to improve it.
It's not going to get any better.
And when we look at me factoring, our
profit margins are between five and 15%.
you're already looking very
close to being in the red.
Just to start with.
And your profit margins
are only 5 percent?
And you don't want to try to
improve that to make it better??
You don't want to take in any of the
data from all of your machines and all
your systems and try to see where you
can improve your efficiency so that
you can get a better profit margin.
And that's kind of my argument against
it a lot of the newer machines, they
have a ton of bells and whistles and
that's already complex in itself.
But if you're not trying to take the
data, you're really not trying to
improve your business in the slightest
,because you're not trying to take
in all the things that allow you to
measure what your performance really is.
Denis: Yeah,
.
I think we had a very interesting
discussion that began all the way from
the bottom of the automation pyramid.
And we
gradually moved up discussing
how the unified namespace can
unify all those data silos.
And what I found personally quite
interesting is that perhaps the biggest
challenges, are not necessarily technical.
We have this generational divide
between let's say the boomers and
Gen X on the one hand who like
things to be the way they are.
And then you have the Gen Zers or
Gen Y even who are younger and can't
identify with their work environment.
But something has to give the final
argument that Brian made, which I
really liked was that look, your profit
margins are really not that outstanding.
Why not just get the data and
measure what you want to improve?
Otherwise you won't.
I think it's a very fair
summary of the conversation.
Is anything I missed you think Luke?
Luke: I think we should ask
Brian you got to ask anything.
Brian: I guess I'll add
some more points onto it.
I think when we're looking towards the
future, what's it going to turn into?
we already can see a lot of the
older generations are leaving.
And we know that it's, a very tough
transition as well as a tough market.
we're very pessimistic about the outcomes
for a lot of these older businesses
transitioning towards this more digital
age we're very pessimistic about the
futures of a lot of these businesses.
That's why we're really trying
to push hard on trying to make
this technology accessible.
Denis: Maybe on that note,
where do you see the data going?
Do you see that they'll make the jump
to the cloud to use AI services there?
Or are you already happy if they just
started looking at the data on premises?
Brian: I think even just on premise,
because the majority of your costs
already is in material and it is in labor.
And most of that labor can be I mean,
you have your overhead that's already
in your business unit, but a lot of the
other costs associated with manufacturing
is definitely the direct labor for it.
If we can utilize and improve the
performance of all of our operators by
giving them the data that they need to
solve their own problems and giving them
the tool sets that they need to solve
their problems, we can already cut.
the costs associated with direct
labor and material costs by
improving the operations themselves.
So there's more or less a glimmer
of hope with it, but yeah.
Luke: Thank you.
It was great.
So it's nice that we end up
with the glimmer of hope and a
positive outlook to the future.
So where can people find more
about you and your services online?
Brian: Yeah.
So you can go to mock controls.
com.
You could email me at B
privy at mock controls.
com, or you could find me on
LinkedIn or even on discord.
If you go to either the United
manufacturing hubs, discord, or
the four pro solutions, discord
tend be in those places a lot.
Denis: We'll put the links
below that in the show notes.
Brian: There we go.
Luke: All right.
Excellent.
Well, thanks everybody for listening.
If you found this conversation and useful.
Join us next time for more smart metals.
If you know, if someone would be great
for the show or you want to participate
yourself, so to those, a message and
we happy to have you on the show.
All right.
So thanks Dennis.
And thanks Brian.
See you
next time.
Denis: Thanks, Brian.
Take care.
Brian: Thank you.