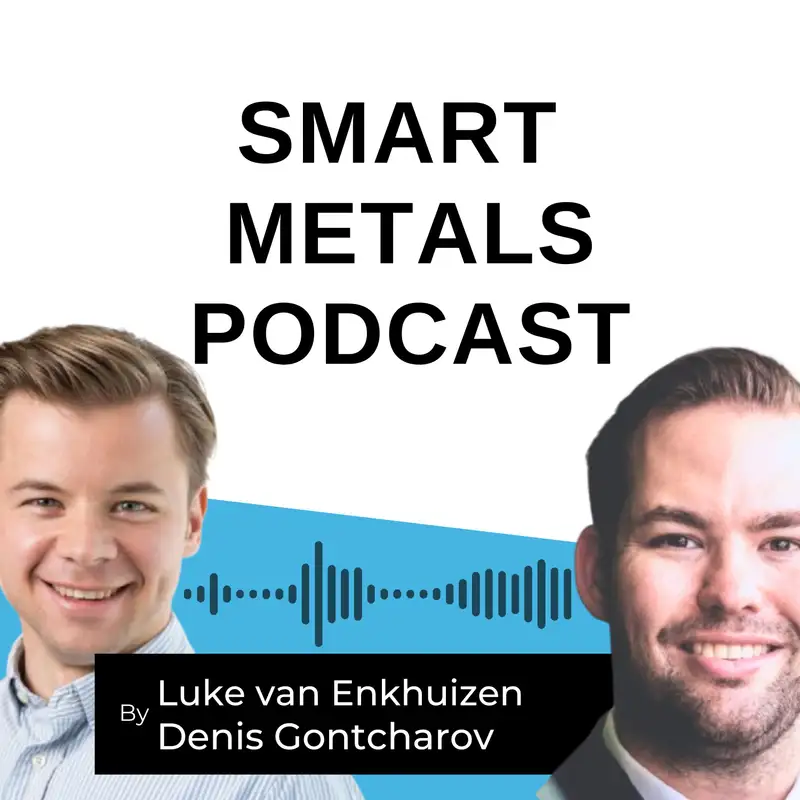
Navigating the Future of Factory Connectivity with Russ Waddell
Luke and Denis: Hey, welcome
back to the Smart Metals podcast!
My name is Luke van Enkhuizen
I'm here together with my co host,
Denis Gontcharov, and we dive into
designing and implementing smart
factories for the metals industry,
helping you become more productive.
And today we invite Russ
Wadell to discuss the important
topic of factory connectivity.
Hey, Russ, welcome to the show.
Russ: Hey, Luke.
Hey, Dennis.
Thanks for having me.
Luke and Denis: So before we dive
into anything, could you briefly
introduce yourself and tell a
bit who you are and what you do?
Russ: Sure.
Yeah,
I my name is Russ Waddell.
I have a company working on
my own, doing a variety of
industrial connectivity projects.
I've been on my own for about 18 months.
That's how I came acRuss
the Smart Metals podcast.
And you and Dennis, actually,
through mutual Online community for
freelancers and prospective freelancers.
So some, I would, I'd kind of
been like poking around the edges.
And another colleague of mine sent
me a screenshot of something that
was in a private Slack and said,
Hey, look at these guys, they're
doing the smart metals podcast.
This seems like it might be up your alley.
After that, I pulled the trigger and
started spending the, you know, I bought
the access to the, to the private chat.
And I think like the first thing I did in
the, the team Slack was like, Hey, Dennis,
Hey, Luke keep going with smart metal.
So this was like maybe episode
two, maybe three at that point.
But I thought it was interesting.
The stuff that I had been doing kind
of related to how do you get factories
down the digital transformation journey?
And from my perspective,
it had been mostly discrete
manufacturing and CNC machining.
And I thought that the first few episodes
that you guys put out in foundry work
and, and metals processing, I was
like, wow, this is like, it's too, you
know, tangentially related segments
of industrial spaces, but the problem
area on the software side of things,
it was like a complete total overlap.
And I'm like, all right,
these guys get it.
They're in the right space.
I should keep up with what they're up to.
And yeah, here we are.
It's maybe a year and a change later.
Luke and Denis: That's
fantastic to hear this.
It's really great to
hear this, this feedback.
Thank you for that.
So yeah could you maybe tell a little bit
more about your background in this field?
Like what were the things that
you were resonating with, like how
did you came to understanding of.
Russ: I mean, I kind of
got into it by accident.
So, I, you know, I studied economics.
I didn't have an engineering background
or education or anything like that.
And I got a job responding to a
job listing in the local newspaper
to go work as an economist.
I worked for the Association
for Manufacturing Technology.
This is basically the machine tool trade
association here in the United States.
I did market research
for them for a while.
It became clear after a couple
years that I didn't want to
be an economist particularly.
I didn't see a path forward for
you know, what that would be
as I was growing in my career.
So I thought I would take a quick Detour
into a path that would get me into some
kind of a software job, and I didn't
have a whole lot of definition to this.
I think I spent enough time visiting
plants talking to company owners
and executives and machinists and
everybody in kind of industrial spaces.
Going to trade shows, reading the B2B
publications, all that kind of stuff.
And I liked the industry, but this
was probably 2010 2012, and, it
was pretty clear that there were
computers running factories, but.
All of the, all the software was kind
of bad and nothing was on the internet.
And I thought to myself at the time,
I'm like, there's gotta be, there's
gotta be like a business to be had here.
There's, there's, there's
room to drive improvements.
This is, nobody was talking about digital
transformation with those words at the
time, but that's really what it was.
And so, you know, the last 10
years have basically been trying
to follow through on that.
So I would, I have a very broad kind
of view of what I'm interested in.
But it's, get the factory software
and networking and drag it kicking and
screaming sometimes into the 21st century.
And the specifics of what I've worked
on have kind of been, here and there,
but that's the big picture thing.
So I worked for a standards
development organization underneath
the AMT umbrella for a long time.
That was the empty connect Institute
as basically surrounded by software
developers and mechanical engineers.
And I was the, you know, the one guy
without an engineering background did
standards development for a while.
Got into technical writing and learned
a lot about information modeling and
systems design and that kind of thing.
And so it was basically just sort
of trying to be a knowledge sponge.
And that was my whole background.
And then it turns out that if you.
I comment on people's LinkedIn posts
and our brief and try and be informative
and be helpful where you can, and kind
of be yourself and be funny where you
can, turns out that that opens doors too
So I became a part-time LinkedIn
commenter for a couple years and that,
you know, that's kind of part and parcel
with ending up where we are here today.
Luke and Denis: Love it.
Excellent.
Yeah.
So if you focus a bit more on how you
describe yourself, you mentioned that you
focus on, well, on your LinkedIn, right?
Speaking of LinkedIn, but you focus
now very much on manufacturing
software, process improvement,
technical marketing, business
development, and community building.
How did you come up with this selection?
LinkedIn.
Russ: have no idea.
I mean, this was you know,
essentially keyword spamming, and
I was just trying to be accurate,
but, accurate and comprehensive,
but still as brief as possible.
And, you know, like, the shared
community for freelancers talks a lot
about positioning, and, I don't know.
I don't really have my positioning.
I just try and go chase
things that I'm interested in.
So I feel like, you know, as an example,
smart metals, the name is right there
in the title and the subject matter.
Oh, we're going to talk about unified
namespace or we're going to talk
about you know, how do you exist
as a software developer, you know,
when you're one of the only ones
inside a hard, heavy industrial
company, those sorts of topics are.
of interest to me, and then I sort of
look for what are the words that I could
use to describe that, where I'm not
completely making up a new term but it,
it still conveys what I'm interested in.
So I, like, it's a terrible
answer to your direct question.
I don't, basically don't know how
I came up with that list of things.
It, and some, once I started working
for myself, it was sort of, how do
I quote work for somebody, whether I
win the work or I don't win the work?
What are the things I put
into a project proposal?
And then, and then how do I carry that?
Whether or not I get the work, like,
how do I carry that forward to, okay,
well, this is the thing I do now.
So this year I didn't have any
experience doing executive search
or anything like that, or a
fractional CTO type of role, but.
A person was retiring or, or leaving a
post and somebody else brought me in and
said, Hey, I need you to cover and figure
out the new person to fill that role.
So I essentially stepped in
with a past trusted collaborator
and tried to work on, you know,
how do we fill that missing CTO role?
And like, that's not something that I
had done before, but now I've done it.
So now it makes it to the list, you know,
and it may not have made it to my LinkedIn
at this point, but as I quote new work
you know, it's going to be in the back
of my head as, all right, if you need
to do, you know, executive search for
tech and technologically oriented roles
that's now something I got under my belt.
I don't know.
I feel like, I feel like I'm
sort of cheating at that answer.
Luke and Denis: I mean, I think it's just
focusing on the thing that works, right?
In a sense we started quite similarly.
Yeah, sticks.
Yeah, definitely.
And right.
The best way to get started is
just get started and see what
sticks and see what works.
We are also exploring and learning
by doing and starting doing the show
because we are just as curious as you
are properly and we all have different
experiences and it's fantastic to
hear you really come from this.
Standards background because I
feel that standards is really
something that is really praised
as the solution to everything.
But there's a lot of
been learned from that.
I think a lot of lessons can
be learned from the standard
background to come up with systems.
But we also see plenty of examples
where that's not the case.
And I think when we talk about the
main topic for today about factory
connectivity, I think all three of us
will have different ideas what that means.
Right?
And what is that defined as?
And if you talk to a sales representative
of a machine maker or a sales
representative of a software seller or
an entrepreneur on the field, they will
all have different definitions as well.
So I think it's fantastic that you
are with us here today because I
think your broad experience and
looking at other actions will probably
paint the picture more clearly here.
So I think we
Russ: I
Luke, I love the example of how
would a salesperson talk about it?
Because a lot of.
Like if you turn the clock
back 10 years I entered, I was
just looking for a job, right?
Like I thought this would be, you
know, a path to get to, to software.
I knew that this standards development
universe and empty connect where I was
ended up working was more technical and
closer to production than where I was.
But essentially at that time, you know,
I remember people would come up to me
and I would talk about, well, you know,
picture a world where you can get the
the data off of all your factory assets.
And instead of being in, you know,
this, you know, gobbledygook of all
these different proprietary languages,
you're going to have it unified, right?
It's all going to be one
standardized terminology.
And people would look me in the face.
This was 2014 ish.
And people would look me in the face
and say, what would I do with that data?
And like the thought of having the
thought of going into a room now, you
know, I can stand on stage and say, you
know, everybody think about what you do.
If you could just see the data that was
in all of your industrial controllers.
Now imagine what you would do with that.
Hold that in your mind and
everything else we talk about.
It's going to be based on whatever your
favorite use case for all that data is.
And everybody in the room has something
that they're thinking about at this point.
The standardization effort set out
to solve was how you get from, you
know, one software developer at your
industrial company or one it manager
or one executive who's kind of going
down this digital transformation rabbit
hole to how does everybody get it and
how do you make it so that every single
person is out there trying to, you know,
sell stuff at least has a definition
that they're working from, right?
As opposed to being.
You know, like I'm just selling
a machine tool based on spindle
horsepower and, you know, the size of
the work envelope that it can cut in.
Right.
So even, even getting, you know, I
looked at it as how you just raise
the level of discourse to where
everybody's talking about connectivity,
even if it's in different terms.
So the standardization actually comes
kind of like second after starting the
conversation about how do I connect these
computer controlled systems to each other?
Right.
Luke and Denis: Yeah.
I think one potential reason why we
see a lot more interest in connectivity
is the whole AI and data science wave.
Suddenly there is a major use case
for having the data all in one place.
Russ: Yeah, it's a pull, right?
So we had basic monitoring.
Then there was some
prognostics and predictive.
AI is clearly sort of the
next development of that.
It needs inputs.
And the easier the inputs are to
access and the cleaner the inputs
are, the more you can spend time with
your data scientists and, you know,
AI researchers working on algorithms,
not working on copying and pasting
data from different CSV files.
Luke and Denis: Definitely.
So let's uncover the topic
for today a bit more clearly.
So let's talk a bit about the definition
of factory connectivity, because I think
we still have different opinions about it.
And before I think we continue Let's.
Define what does it take for a
manufacturer to, you know, do
the factory connectivity, right?
And how would you describe that process?
Can we start with the question first?
Russ: Oh, I have to go first?
Luke and Denis: Yeah,
or shall we start first?
I mean, I can tell from my perspective and
I think of factory connectivity because
coming from quite an IT background, I
tend to immediately think about connecting
systems, all the different data.
But maybe that approach is wrong.
I mean, perhaps it makes more sense
to look at it from a business lens.
Russ: No, I'm with you, Dennis.
I think of it as systems.
I think of it as, you know, does
it have an internet connection?
Does it have a network
connection of any kind?
You know, thinking is as simple as if
I've got all these things that have
an Ethernet port on them, but there
is no communication between them, why?
Right, that's your factory connectivity.
So, is there a wire plugged
into the Ethernet port?
What's on the other end of the wire?
Is the thing on the other end of the wire,
you know, one to one, or is it one to
many, or is it connected to the Internet?
You know, those are the, those
are the sort of connectivity
questions that I'm asking.
Really basic stuff.
Luke and Denis: What do you think, Luc?
Well, yeah, a factory as a
whole is a system, right?
And the factory has inputs and outputs.
Materials comes in and material goes out.
But you also have data inputs.
What does the customer need?
What kind of orders do they place?
And then there is also an output,
like updates about all the progress
or perhaps you have sent messages.
So for me, if we talk about a factory
connectivity, for me, I see it as
information flows and material flows.
And I feel then for me, it would
really Be both from inside out,
as you said, start each factory.
Can it work its way all the way to the
outlays of the factory where, you know,
you can show progress of orders and
so forth in various systems, but also
from the outside in, as in one thing in
discrete manufacturing, as you said, that
you're active in one major challenge.
I see manufacturers that are in that
field where I'm working in is that
They get work requests, so they get
designs from customers in, in discrete
manufacturing and milling and turning.
And you see often there's
3d models already.
And then the first thing that
companies do is they, they somehow
lose that information in the
process and then reinvent everything
again to start producing it.
So there's many layers of complexity
that also not communicating
outwardly in where you are just
also losing a lot of data there.
So for me, it works both directions.
And I would say connected factory.
Would be not only the machines,
but also the business systems
talking to each other.
And that's kind of where my
focus lies at the moment as well.
So maybe I'm too biased for this
to say that it's mostly that, but
for me, it feels that's where most
discrete manufacturers struggle.
Russ: I mean, a lot of what we're doing
here is picking up the old ISA 95, you
know, hierarchy in the Purdue model.
And so these frameworks for what's device
layer, you know, at the quote unquote
lowest level, all the way up to what's
the enterprise layer at the highest level.
And you know, like there's, there's
all this debate about whether a
hierarchy is actually the way it works
or if things are more, you know, less
hierarchical and more graphy is one
of the ways I've heard it described.
And so I have a hard time thinking
about it as anything other than in
terms of programming and coding.
Like, I'm not a coder by trade,
but I think of it as These
are abstraction layers, right?
So how far have I abstracted
away from the device?
So you're talking about, you
know, stacks or layers in a
stack of an enterprise buildup.
But I also look at it as, you know, if
I have one electrical signal that's a
voltage, you know, that's the lowest
level of abstraction or one bit that's
the lowest level of abstraction.
Then how do I get further and further
away from that and make it so it's I'm
interacting with more and more complex
things that, still are in a hierarchy.
But they make it easier and easier to
interact with, you know, say a library
instead of an individual signal.
And so that, that type of stack
up has been really helpful.
I don't know exactly how it ties, you
know, straight to networking and, and, you
know, plugging this thing to that thing.
But that, that type of up and down a
stack or navigating through a graph or
a data model or a, you know, ecosystem.
Those, I think those are the
types of thinking that are part
of digital transformation overall.
So getting to where you have, you know,
everybody in the company is able to, At
least start to interact with that, that
sort of systems approach to thinking.
I think that's what a lot of digital
transformation and digital maturity is.
It's not so much like we have
more devices that are more, you
know, connected in the sense that
they're plugged into the internet.
It's have we, have we
evaluated from sort of a.
Manufacturing and
engineering point of view.
Have we looked at where the
interfaces between things are?
And are we extracting business
value from those interfaces?
Or are we optimizing those interfaces
for you know, for our production
goals or for our business goals?
So it's all like, it's
all kind of tangled.
And I think Luke, to your point about
standardization, some of The benefit
of frameworks, particularly as you get
to bigger and bigger companies, or you
know, if you're looking sector wide,
it's helpful to have those sorts of
standardized frameworks so that you're
not talking about things in circles
and having big arguments about, well,
what do you mean by definition of
connectivity or what do you mean by this
thing or that thing or the other thing?
Luke and Denis: Well, it seems
to be all agree that it's
mostly a technical problem.
So it's really the act of connecting
all the systems in your plant, not
missing anyone and having all the
data available for anyone to use it.
Yeah.
I wouldn't say that it's primarily
the technical problem from a I would
say a four, four, I would say it
depends on this, I think the size
of the maturity of the company.
Because first of all, they have to
kind of know that they need something.
They have to know they
need that data as well.
You need to know what you
want to do with it first.
But how do you know what
you want to do with it?
You need to first.
Learn about the possibilities and have
some small scale successes, right?
So many of my clients that I help in the
sheet metal fabrication industry, they
are not even remotely aware of what it
even means to read out their machine
data and what they can do with that.
If you have the typical, you know, state
charts where you can see if the machine
was on, off, waiting, disturbed, whatever,
for multiple workplaces in one screen.
If you show this to them the first
time, their eyes light up like,
whoa, this is so interesting.
And then if you then tell them that,
you know, their workload is going to
drop if they keep going like this.
if they, You know, they might
have some work running behind a
schedule because of these delays.
And you can visualize that for them.
Then they start to understand the need.
So, and then suddenly all doors open.
So for me, it's, that's one problem.
But then the second problem, funny
enough, in my experience, it's
not even to say that the machine
doesn't have the connectivity.
It's that it's hidden behind
some kind of black box.
That's for example, as
we all know, OPC UA.
Many machines come with OPC UA.
They even have it already,
but the vendor doesn't.
Open it up for do the company
themselves to access it, right?
You need to then buy additional
modules to subscribe to that data.
If it's there, it's poorly
documented and so forth.
So these problems are
really not technical.
They're more political and
more like, like social.
I would even say like, you know,
cultural, even in the company before we
even get to the technical challenges.
That's my experience, though.
What do you think was?
Russ: I mean, it's a perfect match.
I think there may be something of a.
A time lag.
So the scenario that you're describing
where the first visibility into a process
and whether it's on premise or remote
monitoring that sort of eye opening aha
moment that's then going to be followed
by like a pretty profound you know,
uptick in capacity capacity utilization.
You know, I think there was a, there was
actually in the United States, at least,
or North America, there was sort of a
land grab where you had these relatively
immature solutions for basic connectivity.
So it's going to give
you stack lights, right?
Red, yellow, green is
the thing running or not.
And there were two different, right?
Sort of entrance into that space.
The one side I would say these are
relatively small startups that are saying,
Hey the age of the Internet is here.
Think of all these things we
can do by outfitting your,
your manufacturing facility.
You know, not acRuss the board,
but in general, these tended to be
companies that were coming, not from
manufacturing in the first place.
Some of them were venture backed.
Some of them were coming from, you know,
the Bay area and these companies would
come in and be like, well, we're going
to solve all your factory problems.
Cause your issue is that your computers
are too old and your software's too bad.
And mostly, you know, that,
that sort of conceit didn't.
didn't fare that well when it hit the
reality of what production looks like.
And these companies that had no hardware
background or didn't have industrial or
heavy manufacturing background ran into
exactly the sort of problems that you're
talking about that are political and
cultural as well as technical problems
but then you had the other side,
the land grab I'm talking about is
basically you have You know, software
that was developed in the, you
know, 80s and 90s and will tell you
stack like colors status reporting.
And essentially you had sales
organizations that developed
with, you know, what's the
next region we can sell into?
What's the next industrial
segment we can sell into?
How are we going to divide this by,
you know, selling into automotive
versus selling into medical device
manufacturing, for example, and
these companies had pretty limited
technical investment, right?
So their product wasn't necessarily
maturing all that rapidly, but they
were quickly gaining market share
because they were scooping up, you
know, new customers that hadn't
been looking at connectivity before.
And then that led to sort
of, that was like sort of.
Round in my time, it was round
one of this connectivity game.
So you really didn't have to have
a sophisticated technical solution.
You had to have enough know how to
be able to plug some stuff in, get
a signal off a machine, put it on
a rudimentary looking dashboard.
And you know, sometimes this stuff
wasn't even being sold as a service
at the time, it would be like a one
time install seat license type model.
And that, you know, That was like five,
seven, 10 years of, you know, basically
how do I hire a new salesperson?
The new salesperson goes out and finds
new prospects that hadn't really seriously
been shopping for this kind of thing
before, or didn't know that it existed.
And, and you could kind of, you could
kind of tell, like you go to a trade
show and you see, Oh, there's a bunch
of people in so and so's booth, but
it's the same exact dashboarding
tool that they had five years ago.
Like nothing has changed on the
dashboarding tool, but they have more
booth space, they have more people.
They're handing out more business
cards and it was basically just
like, let me scoop up these
eyeballs that Luke is talking about.
And let me get more of those
aha moments with more customers.
And I think that in the States
in discrete and in machining,
that's kind of gone away.
And I think that typical, the
typical buyer now is looking for.
I mean, I guess the cynical version of
it back to Dennis's point about AI, the
cynical reading is an executive went to a
presentation, somebody said AI on stage.
The executive comes back and
said, we need to do AI now.
You know, how do I put that in my factory?
Luke and Denis: yeah, yes.
Let the AI control my factory.
Let the AI do the planning.
Let's do the, let's, you
know, let's do it for us.
Russ: Yeah.
How do we do AI, but
also I'm scared of AI.
So,
Luke and Denis: Yeah.
And I don't want it to have all my data.
Yeah.
How to do AI without giving it any data.
And definitely
Russ: AI while making
sure that we're doing it.
Luke and Denis: that's interesting.
So let's assume there is by now a
will to have a data in one place.
So we actually want a connected
factory, yet we are failing at it.
You already mentioned 10 years
ago, they wanted to build it.
We're building it 10 years later.
I think the whole industry 4.
0 has been going on
for more than a decade.
So it seems to be a difficult problem.
Why haven't we yet have any
standards or any method that.
or platform that has solved this problem.
Russ: Do I have to answer this one, too?
I guess that's why I'm here.
Luke and Denis: Yes, Jobo could put you
Russ: Oh, man.
I mean, I, so, failure is
such a strong word here.
I look at it as maturity.
Right, so there is lack of maturity.
Maybe I'm an apologist, maybe I'm looking
at it from how bad things used to be.
But I see lots of companies
that are succeeding to a degree.
And I see lots of companies that are
Stuck or stable or in some cases stagnant.
And I mean, I don't know this, you
said the same thing in machining with
manual versus CNC machining through
the, through the eighties, right?
So the idea that I'm
going to automate and.
You know, the percentage of manual
machines in my shop versus CNC machines
in the shop, that flipped and there are
very few Western, manual shops left.
Everybody has a bridge port, like
everybody has manual machines still
that's not gone and it's not gonna be
gone, but the number of places that are.
Built on the premise of, rows and rows
of manual machine tools with journeyman
operators standing at the machine,
making a number of parts, using their
hands to turn handwheels, that paradigm
has fully shifted at this point.
That doesn't really exist as a thing
in the United States and most of North
America at this point, because the way
that we do production has shifted, you
know, Not fully because of the technology,
but also things like logistics and
material availability and visibility
into inputs and outputs and the rest
of the system to make it so that,
you really don't have to have that,
you know, fully manual process anymore.
And the rest of the industry has
largely caught up, but the next
wave of you know, industry 4.
0 isn't super well defined as part of
the reason that we haven't gotten there.
So it's easy to say.
Well, we failed to reach the factory of
the future because this, this, and this,
you know, are still backward looking or
they're still archaic or there are still
manual processes or there's so much paper
that still exists on the factory floor.
You know, paper is a good example.
I think.
Looking at getting rid of paper in
a plant or in a physical process
of any kind, I think that can
be sort of a red herring, right?
So if you think of it as paper is
the enemy, that's the wrong approach.
If you look at it as paper is
not a good permanent store of,
you know, the system of record.
That's different, right?
So if I have, you know, me and Luke are
operating equipment and we needed to
get a traveler, but we print out a copy
of that traveler before we start a job.
And then that goes with the job.
And then when there's a change
then, there's a fresh printout
and that's stapled on top.
Now we're looking at a view, right?
So paper is a view as opposed to
paper as the system of record.
The issue becomes, I've got a traveler.
It's going with the parts that are
being moved from station to station.
It's got six post it notes on top
of it, handwritten notes, little
measurements that we've, you know,
adjusted on the fly on the traveler.
And now all of that stuff's not reflected
back into any kind of system of record
that only exists on that piece of paper.
But the issue is not the paper,
the issue is the system, right?
So having a system where you have
a temporary store of information
serving as the authoritative
source, that's a problem.
And that's a problem if you have, if
we were looking at a digital screen
as our input, you still can get to
the same problem because you have
an architect of that system in a way
that you have, you know, permanent
store of data versus reported.
ephemeral data source you know,
that's fit to one specific purpose.
So I don't know, I'm going to argue
a little bit and say, yeah, we
failed, but we're also improving.
And also it's a continuum.
And also it depends on exactly
what company you're talking about.
Luke and Denis: Can I take this one?
I love your answer on this one.
I have so many things to uncover
because this is really my daily
bread and butter bread and butter.
Excuse me for my pronunciation here.
First of all, I actually started
my career doing machining by
hand, turning those knobs myself.
So that feeling that never goes
away when somebody talks about
it, it's just the feeling that the
moment you're standing there, Every
little twitch you make in your hand
affects the quality of the product.
You have to pay attention
to every single detail.
The machine has to be perfectly aligned.
All these things, they matter.
And that is really a
great point to start from.
And I think that sort of people also still
gives them a feeling of what they do.
And I think a lot of entrepreneurs want
to keep that kind of similar feeling
when they use a paper travel as well,
is that they, they know it's there.
They can touch it.
They can see it.
And a question I often
get is like, if they.
want to go paperless if that is
forbidden to use paper at all.
And I would say, well, the paper
itself could be something useful.
For example, you can put something to
recognize the product on a barcode or
a photo, but everything that controls
your operations, everything that is
need, need that feedback loop that
you need to make measurements in that
you need to document for later use.
Those things you want to really Capture
as soon as possible in a digital form.
And so to create that feedback loop
and those kind of things to do that
correctly to make those feedback loops.
That technology is actually something that
we only recently started to get at scale
at an affordable rate for SMB, right?
So you couldn't really expose
your ERP system to the factory
floor back in the days easily.
It would have been way too expensive, too
risky, computers would be too expensive,
networking would be complicated.
And you could get some kind of software,
but if you had to buy something, then
with licenses would be way too expensive
for ordinary shops to leverage that.
So I'm actually quite positive.
I'm not saying we failed yet.
I'm just seeing, we have this
exponential growth and that has
been building up very slowly.
And it came from very far, and only in
the last years we are starting to see
that this snowball is starting to roll.
It started to roll slower down the
hill, but now it starts to roll.
Because we have now this major shift that
happened around the world with, first of
all, we have this open source revolution
that really is now growing rapidly.
So that allows people to
get technology very cheap.
Then we have now the large language
models that help us with developing
things more quickly, more efficiently
computing, of course, got cheaper.
We get the global shift scores that
connectivity is more important because we
do have to work more together to be able
to provide the parts we need plus the
globalization help happens, of course.
So in my opinion, I'm feeling.
Yes, we need to hurry up.
Yes, we didn't of course achieve the goals
by the timelines they were, I would say
envisioned to be, but don't we always
have that problem as humans, right?
When we were in the fifties, we also
thought about flying cars in cities around
now, but we also don't have that, right?
But I'm still very positive that we are
actually now seeing the snowball rolling
and that we now have finally the tools to
make it affordable and start doing things.
And they all have to come together,
but I think we're making progress now.
That's my
Russ: It's easy to skip the
stuff that we do have too, right?
So there's no flying cars, but
we have, you know, phenomenally
good video calls, which were also
conceptualized at that time, right?
Like I went back to the future and
they're making a phone call with
a person's head and they're like,
what we have now works for us.
You know, orders of magnitude better
than what was envisioned in the eighties.
And, and the thing that it turns out
that the thing that doesn't work is
just because you give everybody a video
calling tool, like they can't figure
out how to light themselves well, right?
Like, so what we thought was
going to be the problem was, Oh,
I want to see somebody's face.
And then it turns out what the problem
actually is is everybody's dim and has
a weird background and like, they don't
want to see themselves on camera or like,
There's like latency and these, but if my
kids want to talk to their grandparents on
a video camera, they can, and that exists.
And now, you know, that's only
five, 10 year old technology.
And we're all like, yeah, well,
you know, it's, we've, we've
absorbed that into our daily life.
And we don't even think anything about it.
And that has an implication in, you
know, in the factory environment too.
Like I worked for vendors.
I represented vendors for a
long time, but I think a lot
of times, if you look what the.
Vendors are pushing.
It tends to be, you know, promises
of further out technology and
sometimes ignores the technology
that's right in front of their face.
So, you know, you've got somebody that's
trying to do this, this you know, they'll
have like goggles or glasses or something
where you can share video streams and your
hands are still free and you're going to
get remote support for, you know, setting
up a machine tool or something like that.
Well, okay, that's fine.
It's great that you have that platform and
a subscription model for it, but there are
25 year olds who own machine shops that
are just making FaceTime calls to each
other and sharing their setups that way.
And so you're not competing with
another vendor selling the solution.
You're competing with the thing that's
right there in a customer's hands already.
And that type of a solution.
It's hard to package up and then sell.
And it's going to have huge implications
for how work gets done in a factory
environment, but it's not something
that means, Oh, somebody is going to
be the company that solves that thing.
And they get, you know, They get richer
successful on the back of that technology.
It's just another benefit, you know, email
got invented and changed how factories
did business, but nobody, there was not
like the factory email company, right?
This was just the thing that we all
accepted and got swept along with.
And one of my favorite machine shops
that I've ever visited, they've got all
their scheduling is done in Excel and.
You know, it's this big, massive,
complex workbook, you know, one master
view on the spreadsheet, and it's a
relatively compact facility, so it's,
you know, easy for everybody to see
the one screen and the master schedule
lives on, I don't know, it's like 80
or 90 inch flat screen on the wall.
And the cost for that system
was never in the software.
It was never in the cost of the TV.
Like the cost of the TV was trivial.
The cost of the license
for Excel was trivial.
Had they gone with an external vendor
to do all their scheduling for them,
the complexity wasn't going to be in.
Buying the scheduling tool to
show the thing, the complexity
was going to be in like, what does
our schedule actually look like?
What does our scheduler do each day?
How do they fill in the logic for
dependencies and equipment availability?
And there's no way that you could build
a piece of software that tames a hundred
percent of that for every single case.
So, you know, when I worked.
You know, when I worked for software
companies that were basically selling
competing tools to Excel, I was like,
well, you need to, you need to come
in and use the purpose built tool.
I'm not tied to that at this point.
And I would say, look, I
don't care what you use.
Honestly, it will be easier for
you to go from a well thought out
spreadsheet to a custom built tool.
Then it was going to be to go from
nothing to a custom built tool, because
a part and parcel with that custom built
tool is going to be a huge amount of
process engineering that you had to do.
And a bunch of business process
documentation, which you now
have already done for Excel.
So like, if you want to use Excel, use
Excel, there's a bunch of, you know,
there are features that are bad about
Excel that you should use custom built
software for, but it's not the end
of the world that you're using Excel.
You have your business logic reflected
in some sort of documentation.
And that's the thing that
solves your actual problem.
So there's my, I've got
my, I've got my papers.
Okay.
Rant.
And I've got my Excel is not a big deal
rant and you've got both of them now.
Luke and Denis: Well, I agree.
Yeah, mostly.
Yeah.
I'm gonna be a bit more strict and
be the boom man for manufacturing.
I think we are making the
problem bigger than it is.
If you look at, I agree that we don't
have flying cars and that, but we do
have other industries that are apparently
doing just fine with integrating data.
If you look at, for example, banking,
I was thinking the other day about
If you could potentially create
money without anyone noticing?
And the answer is no, you can't.
Because all systems on the planet are
so interconnected in real time, that
there's just no way you can create
money out of nowhere on a bank account.
You would instantly be found.
So if banking can do it,
why can't manufacturing?
Russ: Yeah.
And server farms are another example
that gets brought up all the time.
Right.
So if I have mostly standard.
Production machines.
So maybe it's SMT machines for
making circuit boards or maybe
it's CNC machine tools, or maybe
it's injection molding machines.
They're all controlled by a computer.
They're all on the network.
You know, at some point managing traffic
loads or job load, it's the same problem.
That's already been solved for
server traffic or for telecom.
Right.
And so how do we take the things that
already exist in the telecom space
and sort of apply them to This load
balancing problem, and I've heard a
lot of discussion about it, and I'm
not exactly sure, you know, how long it
would be before that actually happens or
before I would, would kind of be willing
to jump into the dentist camp and say,
all right, we talked about it for a long
time, but it's, it's clearly failed.
And there's clearly some fundamental
difference between a server farm
and a production machine shop.
Luke and Denis: That's
a major question, right?
So there is this story going on and we
are far from it that in the far future,
basically you know, not even so far
future, but it could go really fast.
But like what I was saying, like if
you, most companies that produce parts
for other companies, like suppliers,
Tire 1, Tire 2 stuff, those kinds of
things, they actually really don't
Produce anything in what they would
say that it sounds really crazy.
But so the idea goes, this is kind
of in line with the server park
analogy because they are saying,
well, look at most companies nowadays.
They already don't make the
machines anymore that they use to
produce the parts, they buy them.
So they buy the machines from different
brands, put them together in a building
that they buy or that they lease.
Then they buy or they lease software
systems to control those machines.
Then they connect those things together.
And then what they are bringing
into the mix is basically how to
spin up all these machines and
softwares by some kind of force.
System and they are
creating their templates.
Well, if you're spinning up a server rack
in a cloud, if you're running spinning
up in it, we'll take, for example,
you can do a Kubernetes instance, you
kind of do something similar, right?
So you, you basically you're,
you're buying server racks or
you're renting server racks.
You're buying licenses or you're
renting software licenses, you spin up a
template and everything starts running.
For those that are producing
parts, in its essence, indeed, it
is going in the same direction.
It's not saying that we are there,
but many companies are still
trying to invent their own thing.
But at a certain point, there will be
some templates that work that are proven
that are there, like in technologies
as well, they are like, you know,
they're going to be certain open source
technologies that are going to win,
like MQTC, they're going to be certain
business templates that are tested in
manufacturing for every single industry.
We know what kind of machines, how
they work, they will all run the
somewhat the same kind of software.
And then all of what it takes
is to spin up more of those.
Who can do it faster and
that person will win, right?
And that will be the same as
the AWS we have in this world.
But then I want manufacturers.
So, but we are talking here
about suppliers, right?
So this is for people that supply things.
If you make your own products
or you have your own designs or
like there is, for example, you
really are doing something custom.
It will be harder, but a lot of
manufacturing exists out of suppliers.
And so those, yeah, they are moving in
that direction, even if they know it
or not, even if they like it or not.
But can we say that
they will be templated?
I wouldn't say so, but I think there
is something to be said about it, yes.
Russ: Yeah, I love that example.
You look at 3D printer farms, which are
pretty well documented at this point.
And the question is, if you can, you
know, if you can hot swap a new 3D
printer, because one is down, or you can
just rebalance the load to a different
printer, and the job doesn't care what
printer it's going to, it's simply
routed to some machine in the farm,
the question is, you know, what's the
biggest scale that that can happen at?
And how does it go from Areas where it's
pretty well proven out in 3d printing
and can it go to other processes?
And I don't have enough expertise in
either how those farms are set up or
the other processes to really Make a
prediction for when that's going to happen
but the parallel for is is really tight
between specifically talking about 3d
printer Set up in a print farm environment
Luke and Denis: Yeah, well, a 3D
printer uses CNC code in the day, or
machine code, let's call it like that.
It's more than just C and C
nowadays, you know, C and C is
really coordinate code, like X, Y,
Z coordinates and some parameters.
These nowadays, these things tend to be a
bit more complex than, than that, but in
the end of the day, they run machine code.
And a welding robot
also runs machine code.
And a painting, a coding line also
runs machine code some way or another.
Every machine runs some kind
of machine code and what's the
one thing that we invented as
humanity in the last 3 4 years?
What is that?
Natural language models.
And what is machine code?
It's a machine language.
So if you can take a Python script
and turn it into a JavaScript, you can
turn a machine code from a 3D printer
into a robot that lays the material.
some way or another.
We're not there yet at the initial scale.
There's too much inconsistencies
in it still to do this at scale.
But that's a matter of you
know, reinforcement learning and
training and improving the models.
So at a certain point you could indeed
take a model that is 3D, I guess, and You
can let the systems make a prediction on
which ways you can get to the end result
and Create the code along the way and
then you could technically Hold swap it if
the machine would be feeding the product.
It's just you know, it's a it's
a it's an engineering challenge
It's a systems challenge
To
Russ: your optimism.
I share your optimism, and I hope to, you
know, in equal parts contribute and drive
that and make it happen, and also to some
extent, this is a train that's out of
the station, and all I can do is grab and
hold on and hope to not get thrown off.
Mm
Luke and Denis: of course,
it's going to be necessary to
do things at scale quickly.
I think I said where to see it in my work.
For example, if you have a bending
machine or for sheets, like a, if you
left a laser cut sheet and you bend
it and you have as a shop, you have,
for example, five different machines,
you can already kind of hot swap them.
If you have a 3d model, so you can
generate programs for each of the
machines and then you optimize one.
And then, you And that machine
tooling and move it to the other
ones and generate new programs.
So that's already quite easy
to do, like relatively easy.
Of course, you need to check it a little
bit, but that's a small scale example.
And that is just the start, right?
So the next step, I would say
you would take the code that
these programs are generating.
warning to AI, that's where actually
AI is going to be necessary, useful.
That's actually where I think it
will be as the language models will
be most useful in manufacturing.
The only thing, as I
said, is the accuracy.
So, yeah.
What do you think, Dennis?
Yes?
Or do I take this too far now?
No, it's fine.
I'm just generally quite skeptical
of natural language processing.
So maybe that's just me.
I was more curious about, The first
things we have to do to get there, right?
I think the optimism is there.
The technology is there.
So what are we missing?
What should companies,
organizations focus on to get there?
If you want, I can even start with this
on because I hear the silence in the room.
Well, I think the biggest challenge
manufacturing face is often cultural.
I've worked also in different industries,
from big pharma to more startups, and
you just can't deny when you enter a
manufacturing facility that you're back
in the 80s, or in the 70s or the 90s.
I think a lot of it has to
come from the cultural side
instead of the technology side.
Russ: You know, I'm like a techno
optimist in some ways, but I also
see it as, as demographic optimism.
So I think a lot of the cultural
change that you're talking about,
Dennis, like, it's not going to be a
new manager who comes in and they're
the dynamic for thinking industry 4.
0 manager.
It's just going to be a
changing of the guard that.
You know, the same thing, the expectations
of a new generation of people who enter
the workforce, they're going to have
different level of expectations for
what their work life balance looks like.
They're going to have a different
set of expectations for what the
technology adoption looks like.
They're going to want best in class tools.
They're going to want to have software be
a component of the job, and they want the
software to work the same way that the
software works in their personal lives.
And so the amount of acceptance for
Oh, this is an industrial tool, so
we pay, you know, 400 times what
we would pay for it as a, as a
private, you know, consumer tool.
And oh, by the way, it
also doesn't work as well.
Like, the tolerance for that
just isn't going to be there.
And there'll be, you know, there'll be
workarounds, and the little companies
that are FaceTime each other, that will,
like, spill over into larger companies,
and the large companies will put in IT
policies that say, you can't FaceTime
each other, and we have to use this.
You know, paid, you know,
collaboration tool instead.
And then that will fall apart because
it'll be unbelievably costly and
people will be doing workarounds and,
you know, like it's, it's progress is
messy and, and I think the cultural
shift is going to be messy too.
And that's okay.
And for any individual operator or for
any individual company or kind of player,
it's sort of like, look for the places
where you can make the change now based
on holding Luke's big picture vision,
but also what do I need to solve today?
And I don't know, like a lot of the,
all the cultural change also comes
from just people who are generally
optimistic and like solving problems,
but being optimistic and liking to solve
problems is a manufacturing mentality.
So if you look at the top.
Pick a percent, the top
10%, top quartile, whatever.
The people in manufacturing have always
been, you know, willing to pursue,
How do I solve the next problem?
And how do I, how do I make it
bigger, better, faster, stronger?
And sometimes it's, you know,
the fun of solving a puzzle.
Sometimes it's the fun of new technology.
But the, the, the thing that hasn't
changed is, you know, what's the
continuous improvement mentality look
like, what's the continuous technology
adoption look like, and, you know, how
do you, how do you keep making stuff?
And I'm, I'm super optimistic that people
want to make stuff and they want to
make stuff in whatever the best possible
way they can with whatever the best
possible tools are and a bunch of crummy
manufacturers will go out of business and
a bunch of good manufacturers will thrive.
And that's kind of the
same as it's always been.
Luke and Denis: I think that's
something I can fully agree in,
especially the distribution of
manufacturers that you have at the
top, are essentially already there.
And I think like companies like Tesla.
And then you have this huge tail
distribution that are just kind of
struggling and will probably not make it.
And then you have the middle
who will need a lot of work, but
that's what makes it exciting.
I won.
I think because there is also
like I hear this all the time.
I said, yeah, the, the, the, all
the small ones will not make it.
Only the big ones will absorb them.
And I have a hard time believing
that because it's not about the size.
It's about maturity.
So it can be a small company
can be very mature and a big one
can also be very traditional.
I also lately started to doubt that
assumption more and more as well,
because if they are nowhere, then
they have a kind of greenfield
scenario and they're not so invested.
Because I speak often to manufacturers
and they say, you know, like last
five years we spent half a million
on this new software system and now
we're not going to change it again
because it's supposed to be good.
But it isn't.
And then comes in now a company five, ten
years later that doesn't have a solver.
this headache.
They go to some kind of you know, Odoo
or some kind of software, and then they
get a machine from a cheaper supplier,
and they get an open connectivity
platform to operate the machines with,
and then they have some kind of Node
RED flow, which is also free, and
they do it for a fraction of the cost.
They don't have that history.
They just take what's now currently
the best practice, and they actually
can do some really interesting stuff.
I actually see quite some manufacturers
that have been quite legacy, and they
just take this overhaul approach, but then
they have to let go of that software from
the 90s and just take that massive leap.
And I'm always surprised that they
don't have that, how would you say it,
this ego, this investment in saying,
oh, we already did so much more, so we
must be so great, so thus, therefore,
we can wait a little kind of attitude.
So I think it's just a natural cycle.
And plus, I'm very big on what's happening
now in the free and open source market
that can do a lot of, like, groundwork.
I would still say there's a lot of need
for proprietary solutions, for sure.
But a lot of things can be done.
Way cheaper, way faster in the cloud.
You can spin up certain software
systems in a couple seconds.
Heck, if you need I.
T., you can spin up a server in
the cloud for a couple minutes.
So a lot of things that small
companies can actually do, which
big ones can't, is that greenfield
approach and quickly change things.
So I am more worried about the larger
manufacturers with their corporate
policies and their status quo they call
it continuous improvement, but actually
it's just more management meetings
Right, like real continuous improvement
is really coming from the floor, right?
So yeah, so i'm actually quite
positive for the the middle middle
group there and the smaller ones
Is there anything that we haven't
covered for today that's maybe
related to this I mean we have to
still talk about in this episode
Perhaps one thing I would add for
myself just to circle back on a
very popular topic that we have
nowadays, the unified namespace.
It's not necessarily a technology.
It's more of a philosophy that's being
pioneered as finally the solution that's
sufficiently lightweight and sufficiently
clear for anyone to implement.
So what do we think?
Would this be a potential solution
to the factory connectivity problem?
Russ: I think unified namespace matters
a lot for any individual project, right?
So get your definition of
how am I going to deploy a U.
N.
S.
and what are going to what
are the components going
to be for how I deploy a U.
N.
S.
I think, you know, large
scale industry wide.
I think that it is principles that
have existed for a long time and will
continue to exist in a lot of its
capturing best practices, but having
terminology for it and You know,
basic rules and, and first principles.
I think that's helpful
for specific projects.
So I'm, I'm in favor of it, if that's
a position I'm allowed to take here.
You know, I'm pro UNS and I don't
have much more else to say than that.
Luke and Denis: Yeah, I tend to agree.
In fact, last year I did some
research about the history of the UNS.
In fact, it's quite an old concept.
It's definitely not from the 1010s.
It's even from the previous
millennium, so to speak.
It's just that the technologies
were used different.
The real reason why it became so popular
was the use of MQTT by Walker Reynolds.
But the idea of unifying all data
in one source is certainly not new.
There's a big buzz around
the unified namespace.
So for me, it's just finally
we agree on one approach.
Let's just do it.
Russ: Yeah, I totally agree with that.
Luke and Denis: Yeah, yeah.
And again, open and free.
And just like you make the example
about someone facetiming, someone to
the other side of the world having
a problem with their machine tool.
You can kind of do the same now with
the technology behind this, right?
So in recent history, like 10 years
ago, every country in the world had
its own little software makers, their
own language and their own tools and
their own, and they might use the
SQL databases, but that's about it.
But they used even the column
names there in their own language.
It wasn't really understandable.
You couldn't really talk to somebody
like even 100 kilometers or miles away
from you and asked, assume that they
would talk the same language about.
the systems they're using.
Now you can actually all talk Node RED,
you can all talk MQTT, you all talk
these technologies that are fundamental
of it, like even proprietary softwares
like Ignition now, like there is such
a global community using those basic
building blocks to create what they want.
Like if you want to make a
flow you can, you know, you can
exchange the flow with each other.
You can, you can have a friend on the
other side of the world, like we are
talking now, and I could make some kind
of flow for my factory and then you
could say, Oh, that's a great idea.
I did this with this flow.
How about this?
And that's how I automate my business.
And that's, I think it's a huge
revolution that's going on there.
That's only possible if you
take that approach, right?
If you all take that same common
technology approach that people
can work upon, exchange ideas with,
and have a structure also how you
organize your business so we can
all collaborate and can all connect.
So for me, it's a massive.
Russ: and the boring stuff too.
You know, the things like having
a, Common framework, which sounds
like, you know, tedious, you
know, compliance conversations.
If what that means is that I can
be on a video call while I'm doing,
you know, Google workspaces style co
creation on, you know, the same way
I do that on a word document now, but
I can do that in engineering tools.
I mean, that's a future that I
think is really, really promising.
And we're still at the point where the
boring, tedious, difficult, Infrastructure
stuff is getting solved to get us to that
exciting dynamic future, and honestly,
by the time it arrives, we'll all be
super jaded about, what we can do.
And we'll all just be expecting that we
can work on collaborative engineering
tools and the, kids, 10 years younger
will come in and they'll be like, what
do you mean there was a time when we
couldn't collaborate on a CAD model at
the same time with, you know, from any
computer we wanted to, or our phone.
Luke and Denis: well, let's hope
. So finding aia, RMA players doing this
there are some brands that already
built these kind of technologies.
Yeah.
So it's, exciting stuff and I really
think one thing I could add to this is
that if you want to get young people
to join your company, you should also
point them in that future that they have.
A possibility to develop their own.
Company, right?
They cannot just work in it.
They have to develop it.
They have to change it.
And how do you give them those tools?
Again, it goes back to the kind of the
boring stuff, maybe in the beginning,
but then also having the technology in
place, like the unified namespace, like
MQTT, like all these local solutions
to then allow them To automate and
improve the factory without having to
rely on somebody else that is not in
the factory, doesn't understand the
central business, like they will, right?
So it's super important for me.
Great.
This has been so interesting.
Yeah.
Russ do you have any closing
words maybe for the listeners?
Some words of wisdom or perhaps a
question they should take away out
of this before we close the episode?
Did we forget something?
I
Russ: You know, I wish I did have
words of wisdom, but I guess it just
comes down to progress is messy.
Keep working, don't worry about it.
Luke and Denis: think
those are wise words.
So, Russ, if some of the listeners
want to know more about you, about your
services, about what you do, what would
be the first place they should look at?
Russ: Connect with me on LinkedIn.
It's Russell Waddell.
Send me a DM or send me a connection
request with a note about what you're
looking for, and I'll connect with
anybody if you tell me what you're up to.
And you can find my
website, russellwaddell.
com.
Luke and Denis: A little
bit below in the show notes.
Definitely, we'll be at it.
Well, thanks for joining
us and sharing it with us.
It was a wonderful conversation.
Yeah, I had a good time.
Russ: Hey, thanks so much for putting the
show together and thanks for having me on.
Luke and Denis: All right.
Well, this was one great episode.
And also your listeners.
Thank you for being with us.
If you know somebody that might
be a good fit for the show.
If you feel you have strong opinion
or even a mild opinion, you want
to share with us, please reach out.
We have to chat and learn and discuss.
And podcast.
Thanks.
Bye bye.